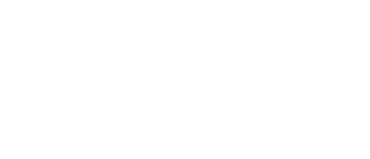
电解制氢系统主要由电解槽、电源、和后处理系统组成,其中电解槽是决定电解制氢系统性能和成本的关键
电极、隔膜是决定性能和成本的核心零部件。压力容器也存在短期供应风险
高活性电极搭配复合隔膜的方形压力槽是碱性电解槽必然发展方向
电解槽的迭代方向服务于:
1)提高安全性(扩大负载范围);
影响电解槽性能的核心因素来自于材料和结构
材料方面:电极和隔膜是影响电解槽能耗的最大影响因素,分别占过电势(除理论电耗的能耗)的 59.7%和 37.3%,在额定制氢量下,复合隔膜(面电阻降至 400 毫欧)搭配新型电极(过电位降 150 毫伏)可降总功耗 15.2%,其中电极功耗可降38%,隔膜功耗可降 56%
结构方面:方形、加压电解槽相较圆形、常压电解槽有更明显性能优势
方形优势:
−更均匀的横截面流场使得气泡可以迅速脱出,不会堆积在圆形流场的两侧造成气泡欧姆过电位上升
−更均匀的横截面流场使得电解槽温度分布更均匀,不会导致电解槽两侧密封垫在高温情况下产生形变造成泄露
−隔膜和极板的剪裁不会造成浪费,圆形的材料损耗率达到 21.5%提高了材料成本
加压优势:
−气泡受压力体积变小,减小气泡欧姆阻抗
−高压电解无需额外在系统最后端加氢气压缩系统,可额外减少系统成本 2 万
搭配高性能电极和复合隔膜的方形加压槽成本相较当前电解槽可降37%
成本降低主要因素:1)电流密度提升带来小室数量下降;2)方形槽带来隔膜、极网裁剪损耗减少
−根据国标 GB 32311-2015: 电流*小室数量/2390 =产氢量,电解槽电流密度的提升可以降低电解槽小室数量,从而降低电解槽成本,经过计算:在 7000A/m2 额定电密下,电解槽的小室数从目前 320 个降至 174 个,电解槽成本从 328.8 万 降 37.1% 至 206.9 万
−由于圆槽横截面为原型,采购隔膜、阴阳电极网需要将方形材料裁剪为原型,该部分材料损耗达 21%