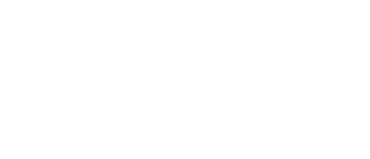
HJT非晶硅镀膜设备
HJT具有产品转换效率高、无光衰、温度系数低、弱光响应高等优点,且由于是双面对称加低温工艺,易于薄片化降本。HJT工序较少,仅涉及“清洗制绒-非晶硅沉积-TCO膜制备-金属化”等四段工序,量产良率较TOPCon大幅提升。但设备投资较大,约4亿元/GW,非晶硅沉积设备价值量至少占50%以上,未来设备降本空间大。
对于非晶硅膜层的沉积,技术上主要分为HWCVD(热丝化学气相沉积)和PECVD(等离子体增强化学气相沉积)。目前来看,主流的技术主要集中在PECVD,只有少数厂商生产HWCVD设备。
一、最成熟、最主流的工艺仍为PECVD
PECVD技术是利用辉光放电等离子体使硅烷等气源分子分解,从而实现非晶硅薄膜的制备。其原理是:反应气体中的电子在外电场中加速获得能量与反应气体发生初级反应,使得气体分子电离分解,从而形成等离子体。等离子体中大量的化学活性的离子、中性原子和分子生成物向薄膜生长表面运输,同时其他产物释放出去,最终形成薄膜。
比较PECVD设备性能的参数有若干项,包括射频稳定性、真空设备完成真空除杂工序的高效性、衬底加热的效率、生产节拍以及最终的薄膜沉积均匀性等多方面。目前各家电池设备厂家仍在围绕设备降本以及提升电池转换效率两方面积极展开研发工作。
二、HWCVD创新工艺可以提升沉积效率,仍存在技术瓶颈
热丝化学气相沉积(HWCVD):从工艺角度理解,HWCVD技术中热丝温度一般在1400℃到2100℃变化。在热丝温度低于1800℃,SiH4原子不能完全分解为Si原子和H原子,还会分解出SiH3基团和SiH2基团。分解出来的原子和基团会向衬底表面运输,在运输过程中,Si原子和H原子还会发生第二次反应,衬底温度和沉积气压不同,所得的产物也会不同,最终得到的Si、Si-H、Si-H2和Si-H3基团是薄膜沉积的主要物质。最终随着表面反应和氢原子的释放,非晶硅薄膜逐渐形成。
HWCVD的一方面优势来源于气体分解主要为高温分解气体,因此不存在PECVD中离子轰击表面的现象,同时更容易产生更多的氢原子钝化晶硅表面,对应的沉积速率也更高。HWCVD的产业化瓶颈主要为镀膜均匀性、热丝耗材。以热丝耗材为例,热丝寿命较短且依赖进口,一方面更换的材料成本高,另一方面更换过程中会对原有生产设备中的真空环境产生破坏,进而导致设备生产效率显著降低。
铜电镀设备
HJT产业化落后于TOPCon的主要原因是非硅成本过高,铜电镀技术可以突破高银耗量的瓶颈,且较丝网印刷工艺可以实现降本增效。成本方面,铜的价格大约只有银的1/100。效率方面,铜电镀相较于丝网印刷银浆可以提升电池片效率0.5%以上,银栅线的细化仍然存在物理极限,但铜栅线可以做到接近15微米的栅线宽度。
电镀铜工艺可以分为“种子层→图形化→电镀”三大环节,每个环节均有较多技术路径可以选择,目前尚未定型。相比银浆印刷,铜电镀最大的隐患在于脱栅,而电镀整线流程中图形化和电镀步骤直接关系到铜栅线的附着力。图形化步骤关系到铜栅线的形状,决定了栅线的覆盖率;电镀步骤关系到铜栅线的均匀性和应力,决定了结构的稳定性。不同的图形化和电镀方法会带来不同的附着力和脱栅率,因此不同设备公司在方法的选择上也各有不同。
种子层制备设备
目前种子层的主流制备方法为PVD,在HJT电池制备过程中,种子层沉积可以和沉积TCO薄膜采取同一台PVD,通过增加腔体数量的方式实现,也可以直接增加一台PVD设备。
目前也有厂商在实验无种子层电镀方案。2022年9月,迈为股份联合澳大利亚金属化技术公司SunDrive采用迈为自主创新的可量产微晶设备技术和工艺研制的全尺寸(M6,274.5cm²)N型晶硅异质结电池,其转换效率高达26.41%。在电池的金属化方面,SunDrive优化了其无种子层直接电镀工艺,使电极高宽比得到提升(栅线宽度可达9μm,高度7μm)。无种子层电镀的优势在于节省种子层制备的成本,但劣势在于其栅线铜应力更大,容易导致脱栅,因此会进一步提高对电镀设备的要求、工艺难度较高,同时无种子层电镀需要将硫酸铜药水更换为碱性药水,因此要求掩膜具备抗碱性,从而抬升掩膜成本。
图形化的主要作用是在掩膜上形成栅线图案,从而在后道电镀工序中能够实现选择性沉积。一般来说,图形化工艺的核心设备为曝光显影设备。
曝光显影是将所需图形转移到感光材料上的过程。在采用干膜贴合、湿膜印刷的掩膜工序后需要使用曝光显影进行图形化,目前曝光显影选取可采取的工艺方式包括:①掩膜光刻+显影、②激光直写+显影。以下就主要的曝光设备做介绍——
掩膜光刻:掩膜光刻由光源发出的光束,经掩膜版在感光材料上成像,具体可分为接近、接触式光刻以及投影光刻。相较于接触式光刻和接近式光刻技术,投影式光刻技术更加先进,通过投影的原理能够在使用相同尺寸掩膜版的情况下获得更小比例的图像,从而实现更精细的成像。投影式光刻在最小线宽、对位精度、产能等核心指标方面能够满足各种不同制程泛半导体产品大规模制造的需要。但其劣势在于掩膜版和光刻机的成本较高,一般用于集成电路行业,无法用于光伏行业大规模生产。而接近、接触式光刻在精度上往往不能满足电镀铜要求的线宽要求。
激光直写(LDI):一种无需掩膜版(光刻机内所需的用于记录图形的掩膜版)的光刻方法,计算机控制的高精度激光束根据设计的图形聚焦至涂覆有感光材料的基材表面上,无需掩膜版直接进行扫描曝光。直写光刻根据辐射源的不同大致可进一步分为两大主要类型:一种是光学直写光刻,如激光直写光刻;另一种是带电粒子直写光刻,如电子束直写、离子束直写等。其中带电粒子直写光刻技术的生产效率较低,且在大规模生产中会产生较为严重的邻近效应;激光直写光刻技术受限于激光波长,在光刻精度上不如电子束、离子束等带电粒子直写光刻技术,无法满足高端半导体器件制造的需求,但在光伏领域较为适用。目前激光直写的方式在光伏电镀铜领域更被广泛关注和应用。
曝光显影之后,电池表面不需要被电镀的部分被掩膜保护,而在掩膜开口处和种子层上方,则通过电镀的方式形成了铜电极。
电镀铜的基础原理:电镀技术是利用电化学方法在导电固体表面沉积一层薄金属、合金或复合材料的过程,是一种特殊的电解过程。电镀铜的具体过程如下:将需要镀铜的基体材料作为阴极,将铜板作为阳极,二者放置在电镀溶液中。阳极的铜板失去电子成为铜离子溶入电镀液中,而阴极的待镀基体表面获得电子形成铜镀层。
光伏电镀的方式包括垂直电镀、水平电镀、花篮(VDI)电镀等方法:
垂直电镀:又称挂镀,使用夹具夹上电池片后浸入含铜离子的药水进行电镀。挂镀技术在PCB应用已经很成熟,但由于需要夹具,如果电流过高会导致硅片表面电势不均匀,从而影响电镀的均匀性,生产效率较慢。同时,单片电池的不同区域、不同电池所处的溶液位置不一致,其接触的溶液浓度也有差异,因此会引起产品片内、片间的电镀厚度差异。此外,正因为垂直电镀的均匀性较差,因此最好搭配干膜工艺,成本也会较高。另外,垂直电镀产能有限也是待解决的问题。因此垂直电镀工艺在光伏电镀铜的实际应用中,仍有较多待优化的部分。垂直电镀的主要厂商为昆山东威。
水平电镀:将电池片水平放置后通过传送带浸入电镀液,电池片在槽体中通过滚轮的旋转带动进行水平链式传输,其中一侧滚轮通常为导电材料,电池与其保持接触,形成阴极。水平电镀下,由于电池表面是均匀的接触导电液,因此保障了更好的均匀性和稳定性。同时,在水平电镀下,电镀液通常只需要覆盖住硅片即可,因此电镀液的使用量也得到了显著节约。再则,水平电镀的传送速度更高,生产效率更高,产能也更大。
花篮(VDI)电镀:2023年1月罗博特科与国电投就铜栅线异质结电池花篮(VDI)电镀技术的解决方案达成战略合作,2月双方技术团队完成第一阶段的设备可行性验证,3月双方技术团队进行第二阶段验证;6月罗博特科向头部客户出货了RTA-CPH-4000/24000型号太阳能电池铜电镀设备。
光伏是新能源领域重要的赛道之一,也是全球各国完成“3060目标”和“能源自主可控”的重要手段之一,未来的年市场规模较2022年的万亿市场仍有可观的增速。降本增效是光伏行业发展的主旋律,也是光伏新能源替代传统能源的动力,度电成本(LCOE)是其竞争力的关键衡量指标。
从技术迭代和工艺创新的视角看,光伏的主要技术壁垒在设备端,清新资本长期关注N型电池技术变革带来的设备投资机会。