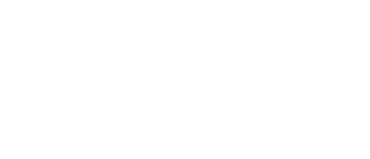
新能源汽车中的三电系统是电动车区别于传统燃油车的核心技术,包括电池、电驱、电控。其中,电池负责提供动力来源,影响着汽车单次充电的续航;电驱动系统主要为整车提供动力,价值量占比仅次于电池;电控则是控制驱动电机的装置,对车辆的运行和动力输出进行控制,如变速、刹车等。本文将以电驱系统入手,从垂直角度分析这一主要产业链上的投资机会,挖掘细分赛道的上行拐点。
基于市场需求驱动的逻辑,我们认为对于该方向所有投资机会的研判最终都应落在经济性、驾乘体验、以及可靠性的三大核心目标上。其中,电驱系统集成化、电机扁线化将是目前主要的两条技术路线。基于分布式驱动仍距规模化应用较远,扁线电机将是当下实现整车综合表现提升的重要技术革新,受益于技术与市场的双轮驱动,是一个从1到n的投资机会。
首先,未来整车形态的发展将由消费者需求驱动。在电动化加速、新能源汽车已大批上路的背景下,汽车产业链技术革新的底层逻辑将是市场对于整车需求的改变。我们可以认为,消费者对于新能源汽车的需求围绕三个核心,即便宜、好开、可靠。市场需求反应到整车设计的终极目标,则可总结为更低的成本、更良好的驾乘体验、以及更高的安全性。
而整车的升级与电驱动系统的演进密切相关。我们都知道,新能源区别于燃油车的核心为三电系统。在电池技术的进步优化了续航后,行业也已经开始关注决定驾驶与消费体验的电驱动系统,目前该领域内最具亮点的技术需要满足上述三大核心目标。在成本逻辑驱动下,驱动系统将走向集成化、平台化、高效率与高转速。而良好的驾乘体验则反映在驱动系统的NVH性能(NVH全称为Noise、Vibration、Harshness,是汽车噪声、振动和舒适性等指标的总称)及其动力性上。最后,驱动系统的可靠性提升将满足用户对于新能源汽车安全性的需求。
在消费者上述几大关注因素的推动下,电驱系统集成化、电机扁线化将是目前主要的两条技术路线。同时,在供给端,集成化与工艺升级的产品价值量最大,产品直接面向主机厂,是行业革新的焦点所在。
1. 电驱动方案:双电机+轮边+轮毂
首先,新能源汽车驱动系统作为三电系统核心组成部分,其发展水平直接决定了整车的可靠性、经济性和驾乘感受。现阶段的电驱动方案按照驱动系统的布置形式分为集中式和分布式驱动布置两类。集中式驱动按照电机的数量可分为单电机和双电机、三电机;而分布式驱动按照电机安装的位置可分为轮边电机和轮毂电机。
图2、新能源汽车电驱动系统将逐步从集中式中央驱动向分布式驱动发展
作为目前的一大趋势,双电机动力系统使用两台电机,分别承担低速和高速部分,兼顾爬坡和续航,其优点是可以提高整车的工作效率、改善动力性、实现轻量化。双电机结构较为简单,技术成熟度高,车型渗透率也在不断提升。然而,集中式驱动与传统汽车相似,具有传动系统零部件多、控制复杂等缺点;与之相比,分布式驱动传动链短、车身内部空间利用效率高,是新能源汽车的重要发展方向。
轮边电机是从集中式驱动到轮毂电机之间的过渡形式,是将电机装在车轮边上以单独驱动该车轮。轮边电机方案下,汽车传动链和传动空间减小,底盘机械结构更简单,整车质量减小且布置更合理,优势体现在提高传动效率、轻量化、降低传动噪声等。目前轮边技术已经在以公交车为主的商用车领域有了较多的应用。从采埃孚最早将轮边用于沃尔沃商用车开始,国内比亚迪、长江客车的轮边电机客车也在2014年相继问世。其中,比亚迪布局较早,它的轮边技术专利量为全球范围内第一。
轮毂电机是分布式驱动的一种终极解决方案,它通过将电机安装在车轮内部,舍弃了很多传统的机械传动部件,大大简化了汽车结构。它不仅继承了轮边电机的优点,而且各轮驱动独立可控,能实现例如360度转弯、侧方停车等操作,颠覆人们的开车习惯。
但是,分布式驱动现在还不能成功切入乘用车领域。这主要是电机尺寸与空间设计的问题:商用车车轮大,利于集成,技术上更容易实现,而如何在乘用车上做到小型化是一个大挑战。轮边电机虽然作为过渡技术走的比较靠前,但是在性能上其实相对多电机而言并没有质的飞跃,未来还会被轮毂电机替代。而轮毂电机的技术瓶颈也不少,首当其冲的便是簧下质量的大幅增加,这对车辆操控性能和舒适度是不利的。此外,恶劣工况可能带来的故障问题也对轮毂的可靠性提出了不小的挑战。分布式驱动的成本也是一个需要解决的问题,其中轮毂电机的价格甚至还要高于轮边电机。在整体系统成本方面,主机厂可接受的价格水平在10万元左右,而现在技术水平较为先进的海外轮毂企业Elaphe在乘用车领域的解决方案单个电机就超4万元,合计单车价值超16万元;另一大公司Protean单电机更高达10万元以上,并不具备产业化条件。总的来说,分布式驱动刚处于起步阶段,需要借助高功率密度的下一代电机技术来顺利实现小型化、轻量化,真正具备应用价值。我们认为,轮边及轮毂电机在乘用车领域的大规模应用还需要等待市场的验证。
2. 驱动电机:从圆线到扁线的平台型技术革新
驱动电机将是整个电驱系统最重要的增量市场之一。我们把电驱动系统向下进行拆解,可以分为驱动电机、电机控制器、传动系统三部分。其中,驱动电机是电驱动系统的核心,也被视为新能源汽车的“心脏”,单机价值量超万元,占整车成本约10%。2021年,国内新能源汽车驱动电机装机量为341.5万台,同比增长133.4%;预计2022年装机量将突破500万台。双电机趋势也会提升平均单车电机数量,预计2025年双电机渗透率将达到25%。新能源渗透率与双电机占比提升的双重驱动力使其未来市场空间潜力巨大;且驱动电机直接影响车辆的爬坡、加速、最高车速等性能,因此驱动电机是汽车产业链改革的核心之一。
驱动电机最大的趋势是圆线电机到扁线电机的技术迭代。新能源车主要使用永磁同步电机和异步电机,其中永磁同步电机低速性能好,转化效率高,国内装机量高达94%。此前,永磁同步电机一直采用传统圆线技术,而圆线电机在市区频繁启停的工况中是低效率运转的。而且,圆线电机的槽满率(指线圈占用槽内空间的比例)偏低,仅有40%左右,这意味着电机的功率密度低、重量大、车的动力也就偏弱。目前,永磁同步电机为了提高功率密度,开始使用扁线电机代替圆线电机。
图3、扁线电机相较于圆线电机在各项技术性能指标上做到了一次革命性的提升
按照上文提到的整车经济性+驾乘体验+可靠性的需求,我们会发现扁线电机能全面覆盖这三大目标,是实现整车综合表现提升的平台型革新。在整车经济性方面,扁线电机能通过将槽满率提升到70%来达到高效率;也能通过输出更高的功率扭矩来提升功率密度,优化整车的经济性和动力性。同时,由于槽满率、效率的提升,铜材用量下降,使得扁线电机相比圆线电机能实现小型化、轻量化,提高了空间利用率、车辆速度及续航。另外,扁线电机降低了齿槽转矩脉动,让车辆能有更好的NVH表现。可以说,扁线电机可以做到全方位的消费者需求覆盖,是继动力电池后另一大技术革新。
从技术端来看,目前扁线方面技术迭代更新快,正处于发展的爆发期。传统的圆线电机相对来说较为成熟,可以沿用工业电机的经验,已经有几十年的积累;而扁线电机的生产工艺有很大不同,且概念提出相对更晚,在过去的一段时间内受制于技术瓶颈。目前技术层面的突破肉眼可见:层数方面,近年扁线绕组技术已由原来的2层、4层升级为最新的10层扁线绕组技术;工艺方面,已由最初的i-pin升级至更为先进的hair-pin路线,博格华纳等tier1厂商也在开发更为先进的连续波绕及x-pin技术。并且,部分国内厂商已掌握设计、制造的核心技术,在生产效率、良品率等方面已达到批量生产标准。可以说,扁线电机正处于爆发的阶段。
从市场端来看,我们预计扁线电机将实现对圆线电机的全面替代,市场空间巨大。在国外,雪佛兰 Volt 与丰田第四代 Pruis 最早开始应用扁线电机。而国内虽然起步较晚,但随着电动化渗透率提高和扁线电机技术提升,比亚迪等主机厂都逐渐将圆线电机替换为扁线电机,增速极快。根据NE时代数据,2022年1-7月扁线电机装机占比高达 47%,比亚迪、特斯拉、蔚来已达到 70%以上;而2020 年扁线电机的渗透率还不到 10%,销量前 15 名的车型中,仅有欧拉 R1、理想 ONE、蔚来 ES6 等部分车型采用扁线电机。值得注意的是,扁线和圆线未来将不是共存关系而是替代关系,目前绝大部分电机制造商的新增产线均为扁线电机,已无圆线产线。也就是说,预计2025年将达到超90%的渗透率,市场空间巨大。
在如此高确定性的趋势下,我们认为扁线电机将成为电驱动系统当前最值得关注的成长板块之一,下文将从制造商、材料端及工艺端分析扁线电机产业链中的投资机会。
3. 扁线电机中游电机制造商
扁线电机的设计与制造商处于扁线电机产业链中游,目前由三类玩家组成。一类是包括比亚迪、特斯拉等在内的具备开发生产能力的整车厂;一类是合资企业,如日本电产和广汽;另一类则是驱动电机的第三方制造商,代表企业有方正电机、华域电动等国内厂商及博格华纳等海外厂商。头部企业多为国际汽车产业链龙头以及上市公司,已具备扁线电机设计制造能力,且有较强的资金投入能力。而且近年来,基于掌握三电核心技术的驱动力,主机厂有自制电机的趋势,对第三方供应商造成了一定的挤压,但未来几年内预计新能源驱动电机市场竞争格局仍然会保持“自产、合资、第三方”三足鼎立的态势。
然而,从初期项目的投资逻辑来看,电机制造商的投资机会较为受限,主要是因为行业重资产与高护城河的性质不适合初创企业切入。首先,电机制造本身是一个重资产行业,再加上扁线电机依赖自动化产线来稳定生产,其设备投入十分高昂,固定资产投入回报期很长。另外一方面,为了实现经济效益,制造商也需要在优化开发实力的前提下获得足够多的订单,来实现规模化量产控制成本。这两点就决定了行业内主要玩家只会是“财大气粗”的主机厂和头部tier1。其次,由于驱动系统是新能源汽车的核心,且扁线电机已从研发试制阶段过渡到批量生产阶段,因此主机厂在选择供应商时会尤为关注其过去在扁线方面的交付经验,初创企业凭借手里的打样和试制线很难打进供应体系。综上所述,电机制造本身有着资金、体量及交付经验上的高进入壁垒,初创企业或新进者在头部企业已掌握扁线技术并拥有先发优势的前提下较难切入市场。
4. 上游扁线电机原材料
扁线电机产业链上游为核心部件及原材料。驱动电机主要由定子、转子、端盖和辅助标准件组成,其中定子组件包含定子铁芯、铜线绕组、引出线和绝缘材料;转子组件包含转子铁芯、永磁体、转轴、轴承等部件,整体占扁线电机成本的50%左右。原材料的性能可以决定汽车的最高车速、加速、最大爬坡度等动力性。
近几年,上游产业链突破技术瓶颈、填补了多项国家技术和产品空白。一些过去依赖进口的原材料与核心部件已实现自主研发和生产,在使用寿命和成本上相较国外厂商形成了差异化优势。诸如稀土磁材、硅钢片、漆包线等拥有核心技术的企业有望大规模增长。其中,稀土永磁材料的成本占比最高,相关公司包括正海磁材、金力永磁、中科三环等;扁线漆包线投入加工难度也较大,龙头公司包括精达股份等;硅钢片变薄也是一大趋势。
电机原材料具有技术+规模双重壁垒,目前行业集中度提升,少数企业掌握价格话语权。首先,材料行业对规模化生产要求高,主要玩家往往具备规模优势和更强的产业链话语权。以稀土永磁材料为例,磁材企业受上游稀土价格波动影响,但龙头企业会将成本变动带来的压力向下游转移, 以保证自身毛利水平的稳定,影响相对可控。其次,规模化采购方式也可压低原料采购价格。另外,扁线电机生产对来料一致性要求很高,因此对于供应商的供货能力也会有所考量。目前,国内稀土永磁行业中具备电机原料供给能力的企业有限,仅有正海磁材、金力永磁、中科三环等少数龙头企业。我们能看出这些多数为上市公司,具备一定价格话语权,因此对于新兴企业来说,想要切入市场有一定难度。
从投资价值角度看,电机原材料在整个电机产业链的迭代升级中处于被动地位,并且产品毛利有限。首先,扁线电机的变革在于制造端在工艺设计上的突破,而不是材料端。并且,材料端平均毛利低于30%,利润空间较为有限,如金田股份电磁扁线产品毛利率约在10%-25%,高性能钕铁硼永磁材料平均毛利在18%以上。
总的来说,上游行业必然会受益于产业链变革。但它的规模化门槛显而易见,而且行业本身得益于扁线技术的发展,不构成行业变更的根本基础,单单依靠材料推动电机技术进步的难度较高。
5. 电机产线设备供应商
电机产线设备供应商会是当前具有极大投资价值的板块,因为产线设备的技术进步直接驱动了扁线的整体变革。虽然扁线电机在很久以前就有积累,但过去它在新能源驱动电机上的应用一直没有推广,缺乏成功经验。相对圆线电机,扁线电机更依赖于自动化产线来达到高效率、批量化的生产。由于各项技术不够成熟,导致产品良品率不高,生产效率低。市场供应商经验和产能有限,在技术和市场层面都不利于扁线电机实际应用。如今国内不少企业已经完成多条试制线、量产线的装配、调试与运行,可落地性得到验证,预计未来会进入起量爆发阶段。
产线设备供应商主要为电机生产商提供智能产线及设备的设计、制造与调试,属于轻资产模式,并且利润空间大。这类厂商一般提供一整套规划、研发、设计、装配、调试、服务的交钥匙工程,商业模式主要分为整线装配及单机设备销售两种,前者单价值更高,平均一条产线价值在大几千万至1亿多元之间,毛利能达到40%左右。这是由于扁线电机工艺技术门槛高,依靠精度更高的自动化设备,因此产线投资额大于传统圆线,设备供应商能享受更高利润空间。如果我们把设备商和电机制造商进行比较,就可以发现,电机制造方在产线上的高投入转移到设备商就变成了高价值。而且,设备商只需要采购零部件进行产线的组装,和电机制造方相比属于轻资产模式。
扁线电机生产设备要求高,过去主要依赖进口,技术较为先进的海外电机产线设备企业包括意大利ATOP、德国GROB、日本小田原等。由于海外厂商布局较早,过去长期以来,我国新能源汽车制造装备的对外技术依存度一直比较高,其中知名度较高的供应商包括意大利 ATOP、德国 GROB 、日本小田原机械工程株式会社和奥地利米巴集团等,技术等级处于一流水平,具有先发优势。然而,国外厂商单线价格昂贵,一条进口生产线平均超过1亿元。
国内电机设备供应行业正在逐步国产化。目前国内新兴企业与传统圆线设备制造商已经攻破了扁线设备制造的技术瓶颈,市场上具备竞争力的一些团队也都具有外资背景和产线设备研发经验。所以近两年可以看到,国产厂商的扁线电机产线订单快速增长,有逐步替代进口产线的趋势。这主要是由于随着国内竞争日趋激烈,新建产线更加注重效率和成本效益。一方面,国产厂商往往具有明显的成本优势,在招投标过程中较具竞争力。另一方面,外资厂商响应速度慢、交付周期长,这是行业都了解的一个痛点。处在快速扩产阶段的tier1企业与主机厂会更倾向于选择具有快速响应能力的国产厂商。
其次,自动化也是未来一大趋势。为了提高电机的效率和功率密度,扁线绕组的层数逐渐增加,线形设计也随着层数升级多样化,客户对定制设备的自动化程度要求随之增加。自动化产线不仅可以节省人工成本、提高生产节拍,也能满足扁线工艺对于产品一致性的高要求。然而,由于自动化工艺概念设计的门槛很高,目前仅有几家具备全自动化产线能力。值得注意的是,由于单线价值高且扁线产线行业还未完全发展成熟,电机制造商会重点关注供应商过去的整线交付经验与质量,因此具有成功自动线交付案例的产线设备供应商会具有先发优势。
结论
以上,我们从消费者需求出发,浅析了电驱动产业链的技术趋势,从整体的电驱动方案,再向下细化到电机自身的工艺升级。电驱动方案板块还没有迈出乘用车应用的那一大步,但是电机自身的升级已经在大刀阔斧地进行中。在整个扁线电机产业链中,价值占比较高的又属电机及其产线设备的制造。在大趋势确定的情况下,产线设备在技术、稳定性上的突破可以带动电机厂商锁定整车客户,充分受益于未来几年扁线放量红利。综上我们认为,在扁线电机行业,兼具较强国产替代属性、技术研发能力与业绩增长动能的“卖铲子”产线设备供应商会拥有强悍的基本面支撑。